Proper Installation of Insulated Metal Roof Panels
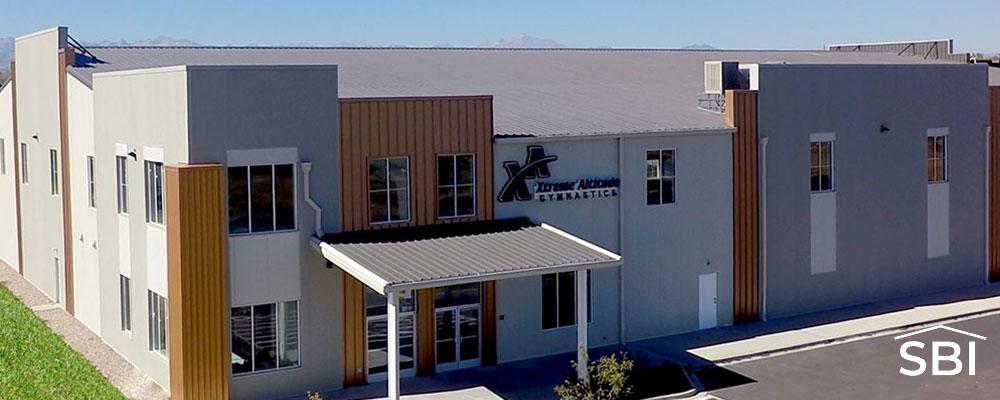
Insulated metal panels (IMPs) are an ideal roofing solution for pre-engineered metal buildings. Long lasting Kynar paint systems hold up very well against weathering and UV fade. They are available in lengths up to 50’, and may also incorporate endlap joints for longer roof runs. Panel thicknesses are from 2” through 6”, with excellent R values of approximately 7.5 per inch.
There are several installation considerations when using IMPs with pre-engineered metal buildings: Structural alignment – IMPs are fairly flexible, but not as flexible as single skin roofs. Typical structural alignment for roof panel supports is 0” inward, ≤ ½” outward of roof plane. Failure to properly align structural components to these tolerances can result in numerous issues:
- Difficulty in engaging panels – upon attachment, panels will follow the contour of roof purlins. As the next panel is laid into place, engagement can become difficult as the original panel is now shaped by structural misalignment.
- Seaming issues – roof leaks may result if panel sidelaps do not align properly due to variances in the roof plane. Standing seam roofs will not seam proper if panels are not properly aligned.
Panel alignment – In addition to structural alignment, panel alignment must be checked often to ensure that the panels do not “dog leg” as they travel from ridge to eave.
Misaligned panels can result in:
- Aesthetic issues, particularly at endwalls where cut panels may have to be skewed to fit
- Endlap joint problems where panel splices are not properly located over underlying purlins and support angles
- Vapor seal issues where splice plates do not mate properly at endlap locations
- Difficulties in properly attaching roof perimeter trims, including gutters
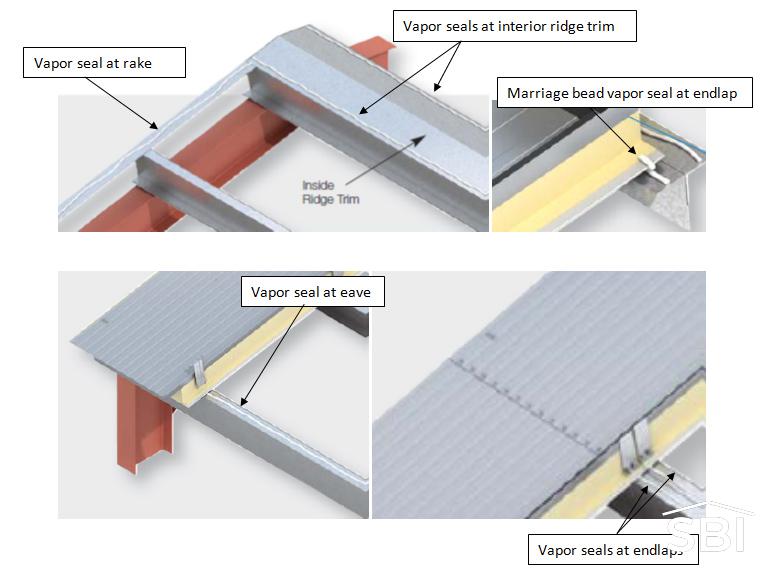
Each of these improper techniques can result in unacceptable panel performance. Properly aligned secondary supports allow panels to engage easily and without undue force, will seam properly, and will provide proper weathertightness.
Sealing locations – are critical when using IMPs. It is critical to remember that there are two sealing locations with insulated panels. The exterior face is where all weather sealing must take place, and the interior face is where all vapor seals must take place.
Weather seals – due to IMP’s composite nature, liner side skin and foam must be removed to access the underside of the exterior sheet at all lapped locations. The following conditions require “shingling” of the exterior sheet for proper weather seals:
- Endlaps
- Roof curb units
- Valley gutters (when present)
Vapor seals – require proper sealant placement to maintain the vapor barrier. Butyl sealant must be placed on top of the structural supports at ALL panel terminations including eaves, endlaps, ridge and rake areas. Marriage beads must also be installed at all panel terminations to tie in the panel sidejoint vapor seals to the panel endjoint vapor seals.
Ridge conditions – are another likely source of roof problems and require special attention for proper performance. Sealant must be placed above and below foam closures, and between the edge of the foam closure and the vertical panel seams. Sealant must also be placed on top of the metal Z closure so that it seals properly to the exterior ridge cap.
In addition, the ridge condition must be fully packed with either compressible insulation (batts) or two part urethane foam. There should be little or no air gap between the exterior ridge cap and the packed insulation in order to prevent condensation.
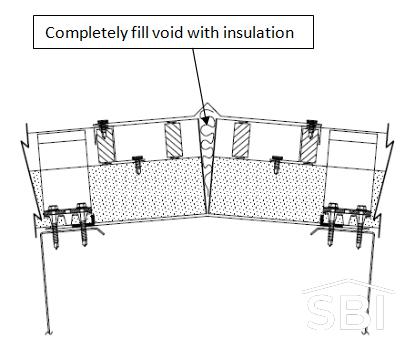
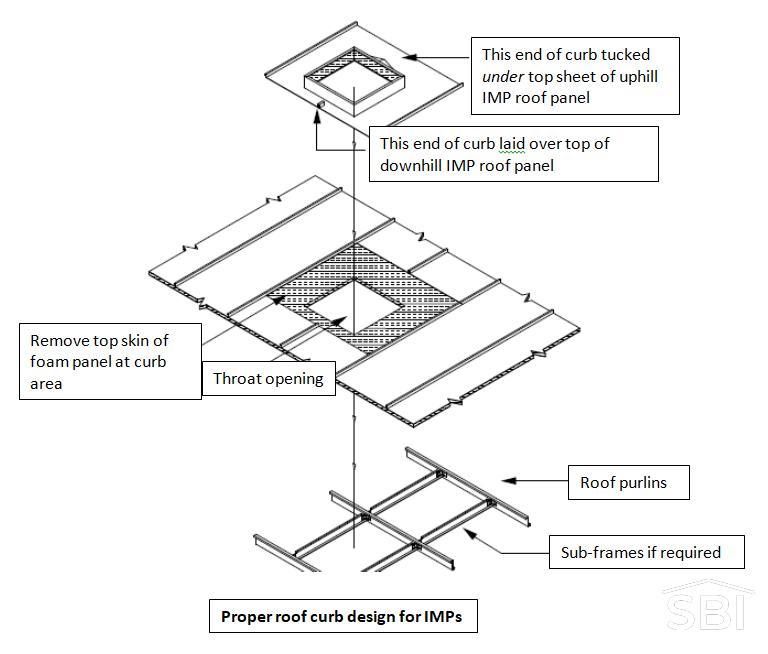
Roof Penetrations
Care must be taken to ensure that roof penetrations are properly designed. The use of pre-formed curb units are highly recommended, especially those that conform to the roof profile being used.
Roof panel penetrations such as skylights, equipment curbs and smoke hatches should be installed with under/over flashing details. The uphill flange of the curb unit should tuck underneath the exterior roof panel sheet, and the downhill flange of the curb unit should lap over the exterior roof panel sheet. Curb units should extend from sidelap to sidelap and mimic the shape of the roof panel including the vertical seams.
Cut panel areas may also need to be supported from underneath with sub-frames whenever required by the panel manufacturer.
Over/over compression curb units though cheaper and easier to install, are not recommended due to over-reliance on sealants.
Pipe penetrations should be properly sealed with dektites (or similar) using compression type fittings. The top of the dektite should also employ a clamp to tighten the boot around the pipe.